膠囊用于多種應用,因此生產量極大。Greiner Packaging的經營歷史已有50年,對于其UPP-“Unique Packaging Proposition”(獨特包裝建議)非常自豪,這能保證他們的客戶每次都提供包裝解決方案。Greiner Packaging目前對其膠囊質量檢驗過程進行了數字化,從而確保公司無需在大批量生產和質量要求之間厚此薄彼。這一創新解決方案的重要部分是ZEISS VoluMax 800 CT測量機。
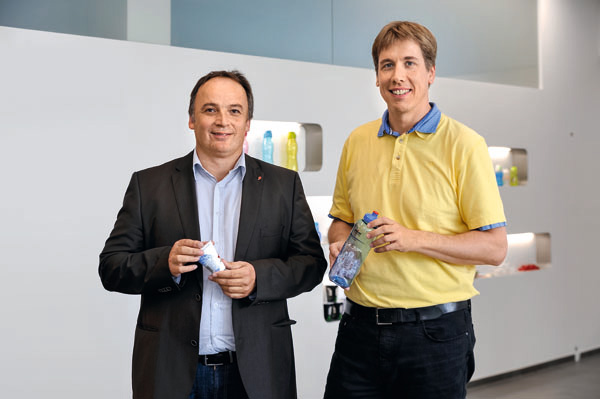
毫不夸張地說,全球范圍的超市和消費者家中有數以百萬的消費品包裝在膠囊中。因此一個產品批次的缺陷就可能導致全球召回,這是每個經理害怕的噩夢。除了造成成本增加,更重要的是形象損失:產品召回導致的大部分價值損失是聲譽的污點。消費者不熟悉也不想知道缺陷包裝的原因,品牌制造商會感受到消費者的憤怒。這導致了自相矛盾的情景:成本僅幾美分或更低的包裝在質量聲譽中卻占據巨大比例。
不間斷生產Greiner的膠囊業務單元位于Krem-smunster小鎮Greinerstrasse的盡頭,Kremsmunster是奧地利北部一個充滿山水田園風光的小鎮,公司的制造和管理單元也位于這里。進入生產區,你能通過無菌斗篷和帽子的顏色區分員工和訪客。員工戴著白帽子,訪客戴著紅帽子,因此能很清晰地分辨出誰在這里工作,而誰只是訪客。全自動的生產線長度超過50米,開始是作為源材料的多層薄膜,延伸到被稱為“深沖”的成型過程,再到包裝箱密封。彼此靠近的多條生產線快速移動和打氣,每年365天,每天24小時生產數以百萬的膠囊。但這些產品要在檢查后才能交付。為了確保每個膠囊都滿足客戶的詳細規格,質量檢查部門晝夜不停地工作。
大幅增加檢查參數“過去客戶為我們提供量規和其它設備,對膠囊進行機械檢查,我們使用這些設備進行各種部分檢查。”質量工程師Robert Pfundbauer說。每個輪班多次將50-70個膠囊從生產線上取下,使用接觸式方法需要檢查總共八個參數,但要求的窄公差和高精度使其成為一項挑戰。質量檢驗員Muhcu Zeynep展示了這些測試程序中的一個。她拿起一個圓柱形金屬量規,將其放入待檢驗的膠囊中,檢查其是否完全匹配。這個過程需要大量時間和精力,如果不正確地觸碰膠囊就會產生壓痕。
客戶的質量要求逐漸提高,這影響了從cpk值到抗壓強度和重量的所有參數。越來越多的參數要根據允許的公差來設定。膠囊業務單元主管Helmut Reckziegel解釋了該產品:“包裝不再是單獨的產品,它已成為高技術含量的功能單元。”因此他三年前就開始尋找高效的質量檢驗解決方案。一種方法吸引了他的注意:一家位于意大利的摩托車外殼制造商使用X射線檢驗膠囊的質量,而且Reckziegel知道計算機斷層掃描成為了質量檢驗方法。
共同開發“我們沒用多久就選擇了蔡司。”RobertPfundbauer回憶到。“我從1990年就熟悉他們的測量機。除此之外,我們還在Kremsmunster使用ZEISS O-INSPECT復合式測量機,還在其它地點使用其它的蔡司測量系統。”因此開始了非常復雜的開發過程,重點是該系統的核心:計算機斷層掃描。這花了一年多時間,因為需要做大量準備,從而使系統能檢驗規定的參數。需要編程復雜的算法,按照客戶要求裝配虛擬量規并創建分析。客戶規定的參數需要分析數據的相應計算能力和傳輸能力。除此之外,檢查過程要求重量測量結果精確到幾百分之一克,進行微米級測量并確保細致和一致的記錄。此外,需要為X射線室開發一種瓶帽支架和底座形式的額外負載后勤解決方案,因為客戶想用一次操作檢查整個隨機樣本。
生產線末端一臺五噸重的機器在15米高的辦公室中間,你會發現一臺ZEISS VoluMax 800連接到高速計算機。這臺CT測量機重5噸,類似一個巨大的柜子或現代風格的大件辦公家具。觀看運行中的系統時,檢查過程本身看起來似乎很普通。每個瓶帽有一個鐫刻的空穴編號。每個輪班分多次從生產線上取下五十個瓶帽,完全按照客戶提供的指令。將瓶帽放在特殊設計的支架中,放在適當的底座上,然后將這個“瓶帽塔”移動到X射線室。支架和底座由蔡司設計,采用特殊塑料,不會影響或降低掃描過程。輸入生產數據,關上門,按下啟動按鈕-大功告成!“我真的很吃驚,”Zeynep說。“現在所有工作都更加簡單、快速,而且重要的是精度大幅提高。”這個系統使用X射線輻射至少不會擾亂她。首先,這個系統采用聚合物混凝土和鉛屏蔽。第二,只有關門時才產生輻射。國家安全防護部門也測定“檢查辦公室中沒有任何放射性痕跡。”
隨機樣品在X射線室中留存半小時。在操作員監控五十個彩色圓圈的屏幕上,每個圓圈對應一個試件。如果圓圈是綠色,則一切正常。如果其中一個圓圈顯示為紅色,則操作員立即知道哪個參數沒有滿足。十二臺單獨編程的計算機在環境中運行,實時顯示結果。對應的PiWeb軟件也來自蔡司。以客戶規定的格式生成各個測量的報告。
由于包裝問題導致的召回近乎不可能該公司自2016年7月就使用ZEISS VoluMax 800。當問Pfundbauer他目前對這臺機器的性能是否滿意時,他的自豪之情溢于言表:“這個系統讓質量經理的夢想變成現實。”雖然試驗階段有很多復雜的狀況,但都是由于IT問題導致的,而非CT測量機本身導致。同時Pfundbauer還強調,蔡司立即解決了這一問題。現在通過遠程維護聯系蔡司,同時Greiner仍對機器完全控制。
曾經檢查8個參數要用45分鐘,而現在半小時就能檢查16個參數。除了裝載和卸載CT測量機,不再需要稱重或測量等人工操作。乍一看,這個解決方案似乎能在質量檢查中達到人工效率的三倍。這當然令人向往和激動,而且還能降低成本,但對于Pfundbauer來說,生產量增加并不是重要的好處。對他來說,重要的是安全性,因此問題應該這么問:“由于包裝而導致召回的可能性有多大?換言之,Greiner客戶的情況可能性有多大?”由于這些天測試的參數量是過去的兩倍,而且精度遠高于過去,這種可能性幾乎為零。
不僅是增值通過計算機斷層掃描連續一致地記錄每個批次還有一個重要好處:如果某個點發生問題,可以立即排除是包裝導致的缺陷。例如:生產鏈條下游的裝瓶設備接收每個交付批次的所有相關文件。只需輕輕按下按鈕,就能獲得這些文檔,而且所有規定的參數都有清晰的校驗標記。Greiner員工無需再花大量的時間填寫表格,而且消除了意外輸入錯誤導致人為錯誤的風險。產品上自動讀出的空穴編號直接傳輸到相應的文檔。
還有另一種有利于CT測量機的聲音:和其它任何工具一樣,生產瓶帽所需的深沖工具具有規定的使用壽命。微米范圍的磨損跡象意味著這些工具只有超過特定的限值時才會更換。然而,過去要檢查是否超過這些限值,需要進行人工測量,Greiner現在很早就確定產品偏差是否在公差內,防止其影響生產質量。這使公司能夠更好地規劃維護作業,降低由于生產意外中斷導致交付能力不足的風險。
借助蔡司的這個解決方案,Greiner不僅能踐行其口號“做出創新”,而且成為在生產量極大的情況下優化數字質量檢查和質量保證領域的創新者。這種以ZEISS VoluMax 800為核心的端到端解決方案在包裝行業設定了新的標準,而且Greiner公司內部也對其它應用領域展開了廣泛討論。Reckziegel這樣總結公司的體驗:“它并不只是測量機,而是完整的解決方案。只有蔡司能幫助我們解決這個挑戰。”
Greiner集團該集團于1868年成立,當時是德國斯圖加特附近村莊Nurtingen的一個雜貨店。Here Carl Albert和Emilie Greiner開始用軟木塞密封蘇打水瓶。Greiner在1878年世界博覽會上購買了軟木塞切割機,開始將瓶帽生產轉化為向第三方提供的服務。今天,Greiner集團是世界塑料和泡沫材料行業的領先者。該公司持續實施多樣化、創新和全球化。Greiner的經營范圍包括包裝、家具和汽車工業以及醫療技術和生命科學領域。“瓶帽”業務單元是Greiner Packaging International旗下的部門。該業務單元有大約4000名員工,在32個地點為食品行業和非食品行業的成功品牌生產獨特的包裝解決方案。